May 20, 2025
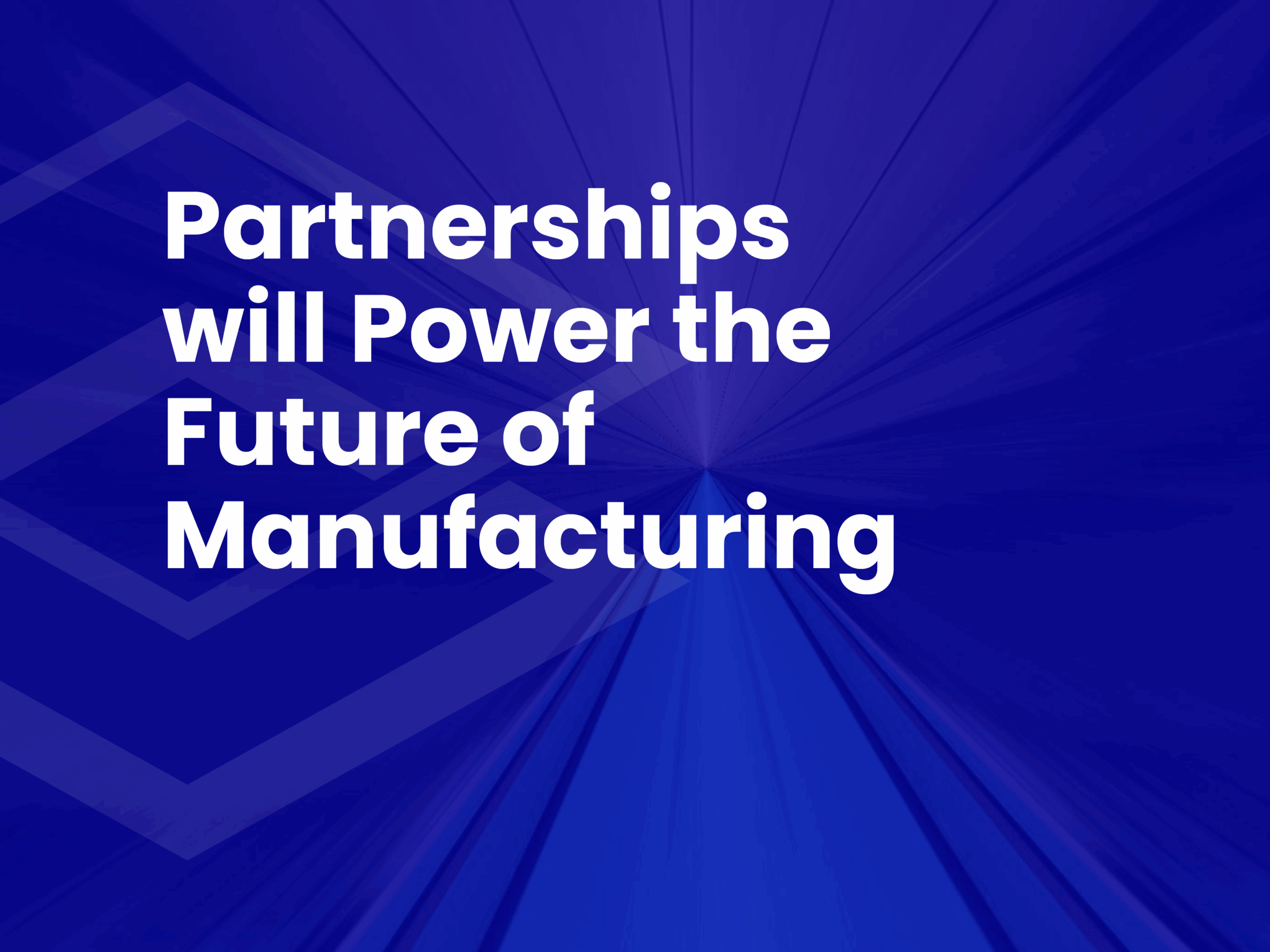
March 18, 2025
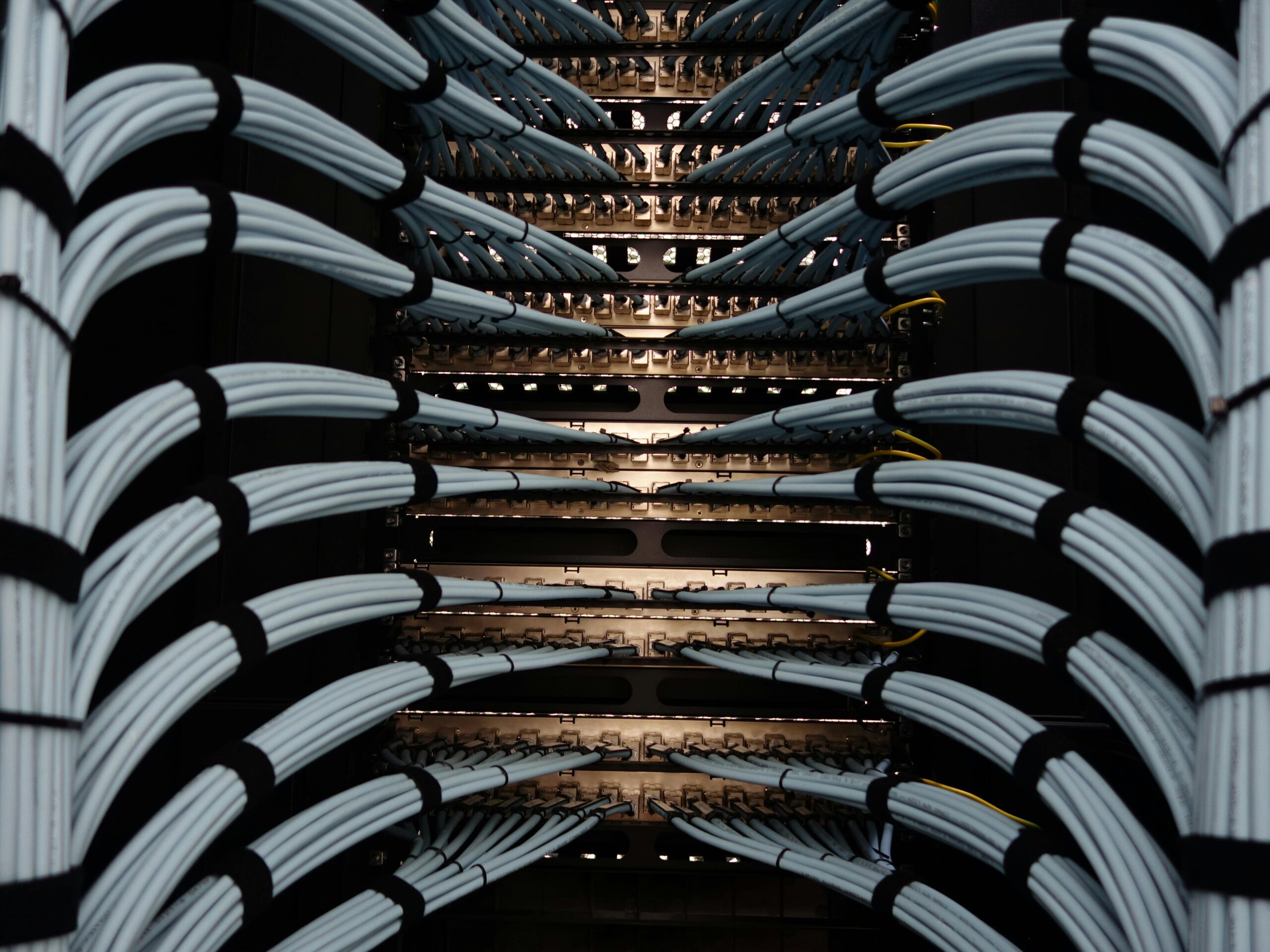
March 11, 2025
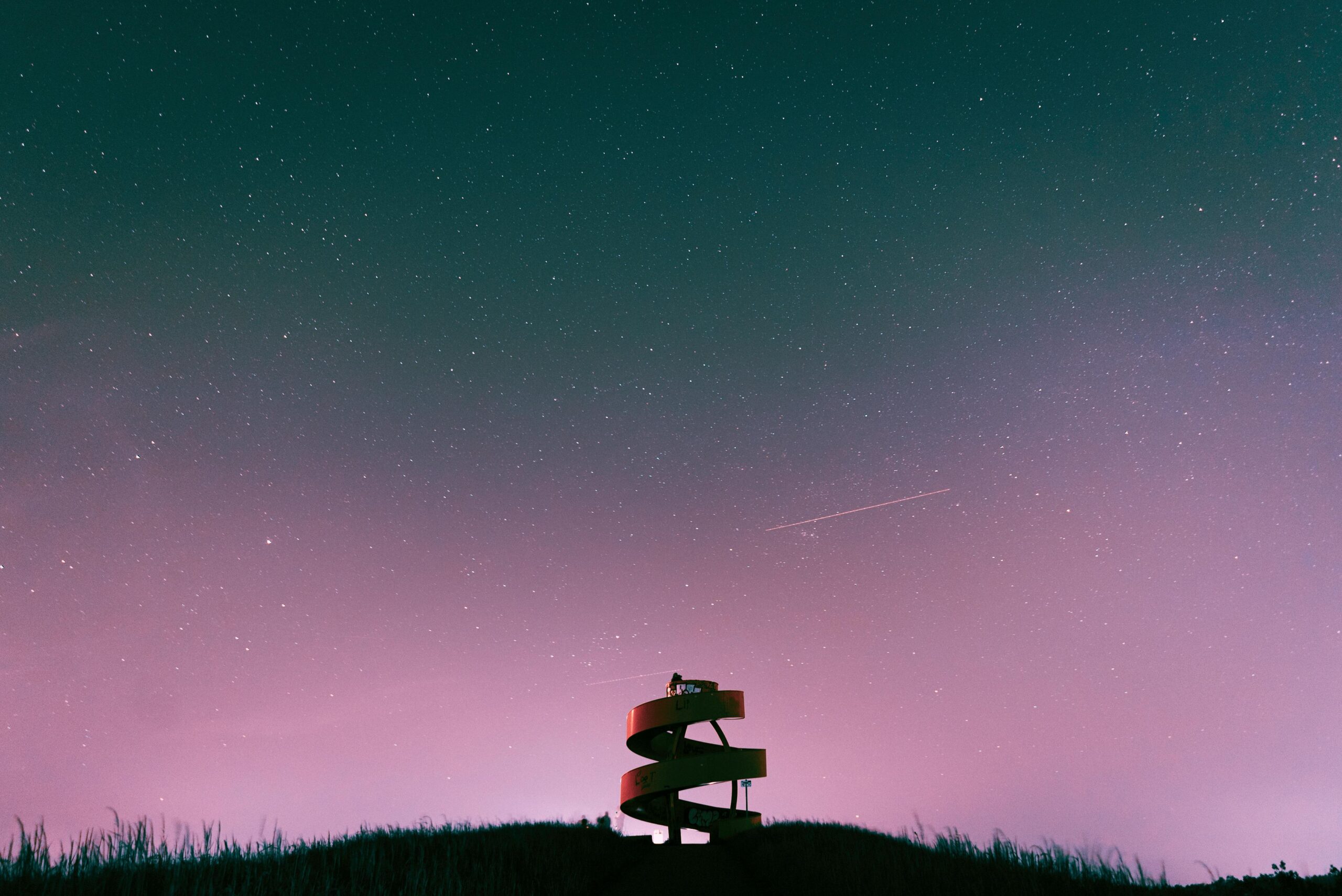
December 9, 2024
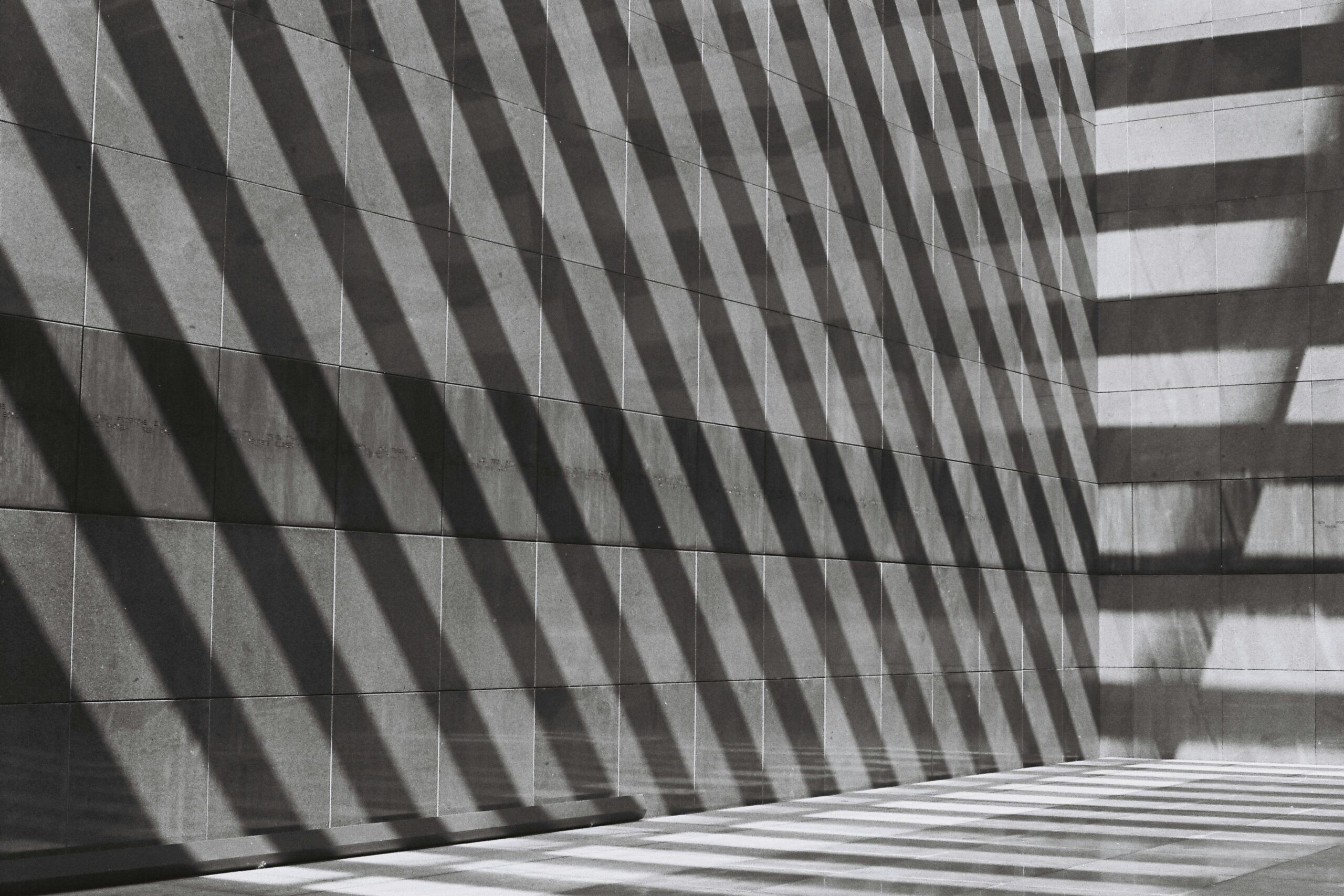
October 15, 2024
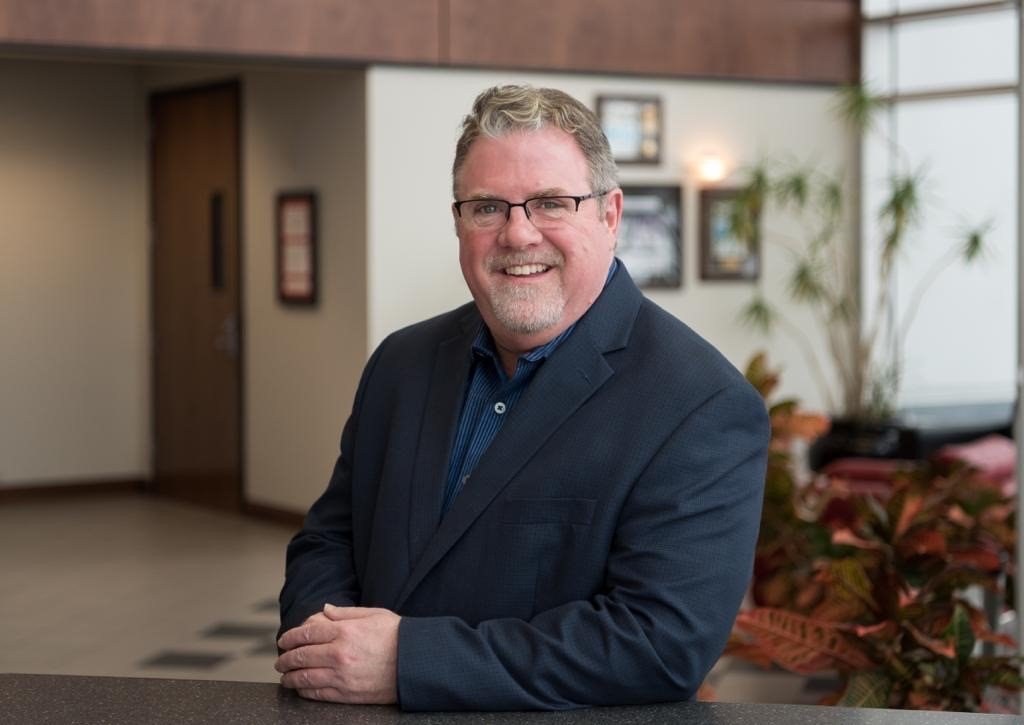
September 6, 2024
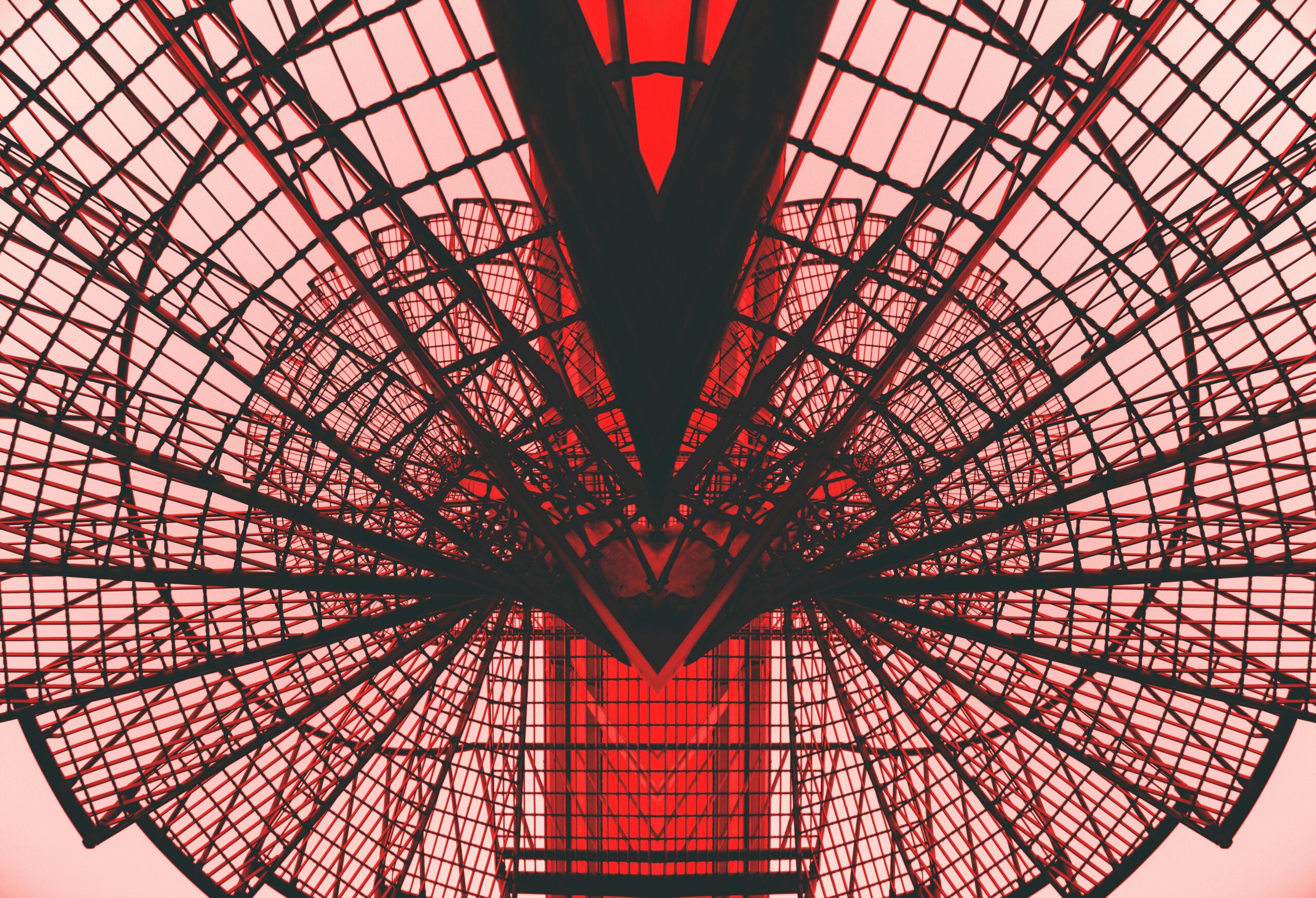
September 4, 2024

August 27, 2024
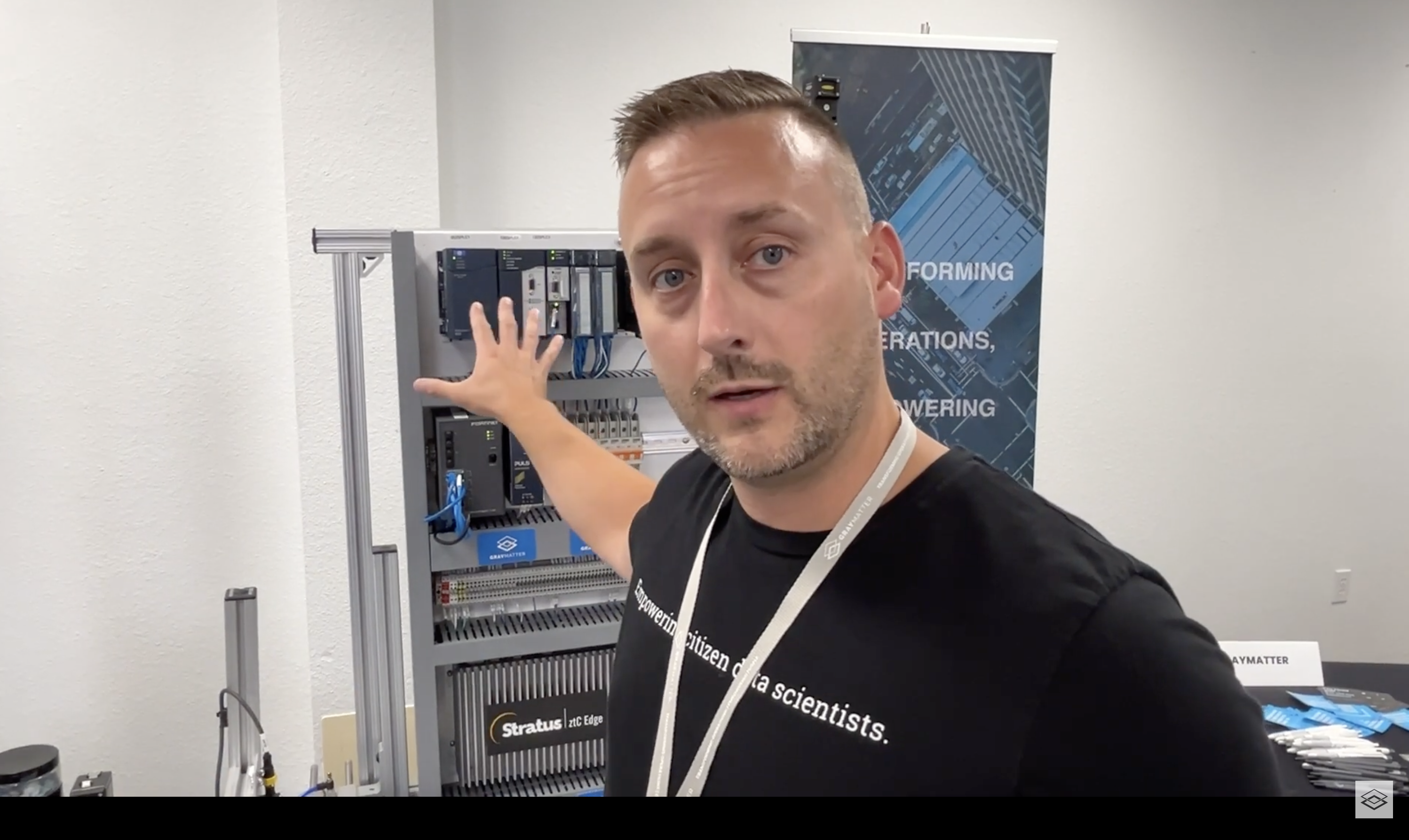
July 19, 2024
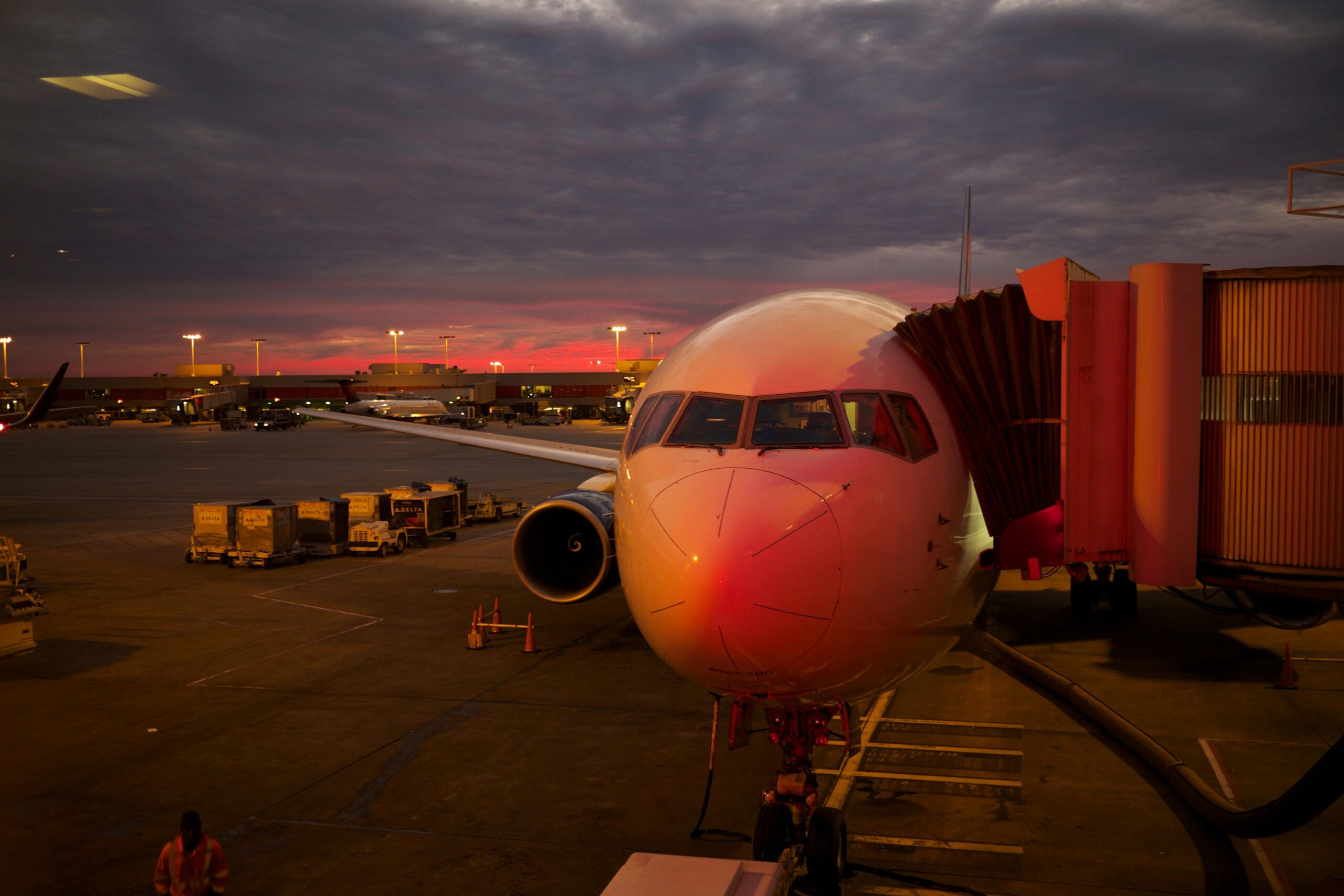
June 25, 2024
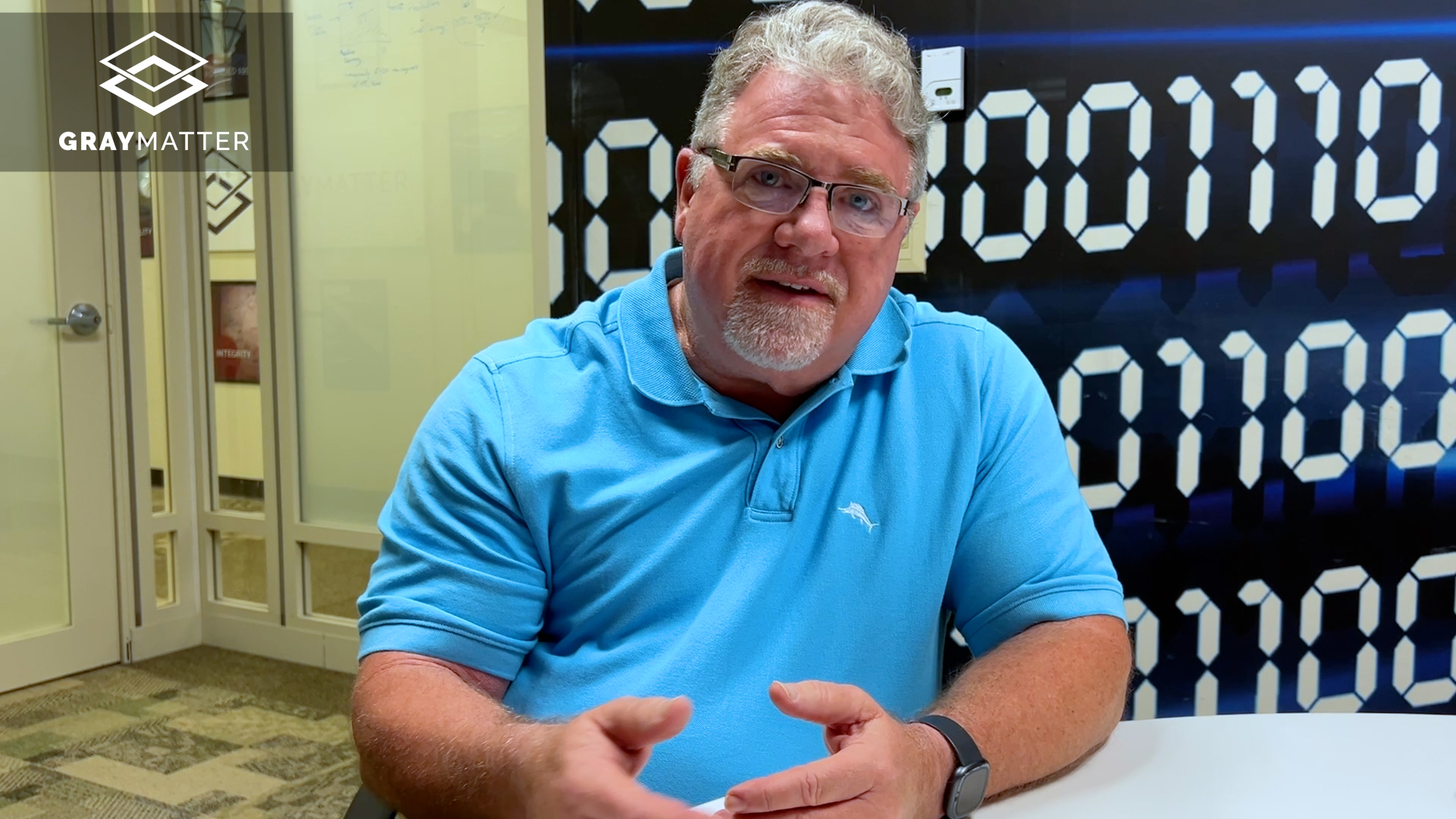
May 16, 2024
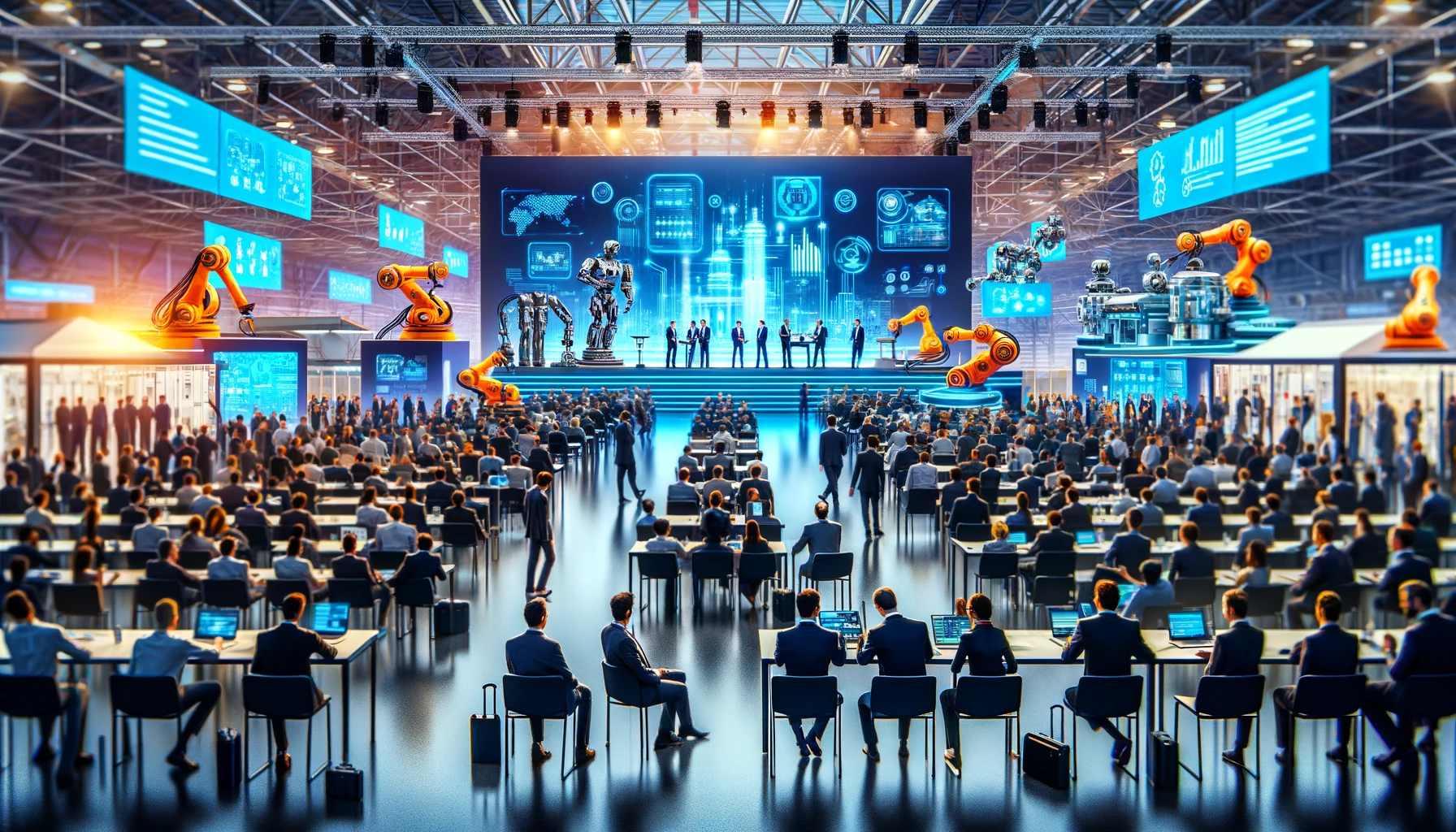
April 18, 2024
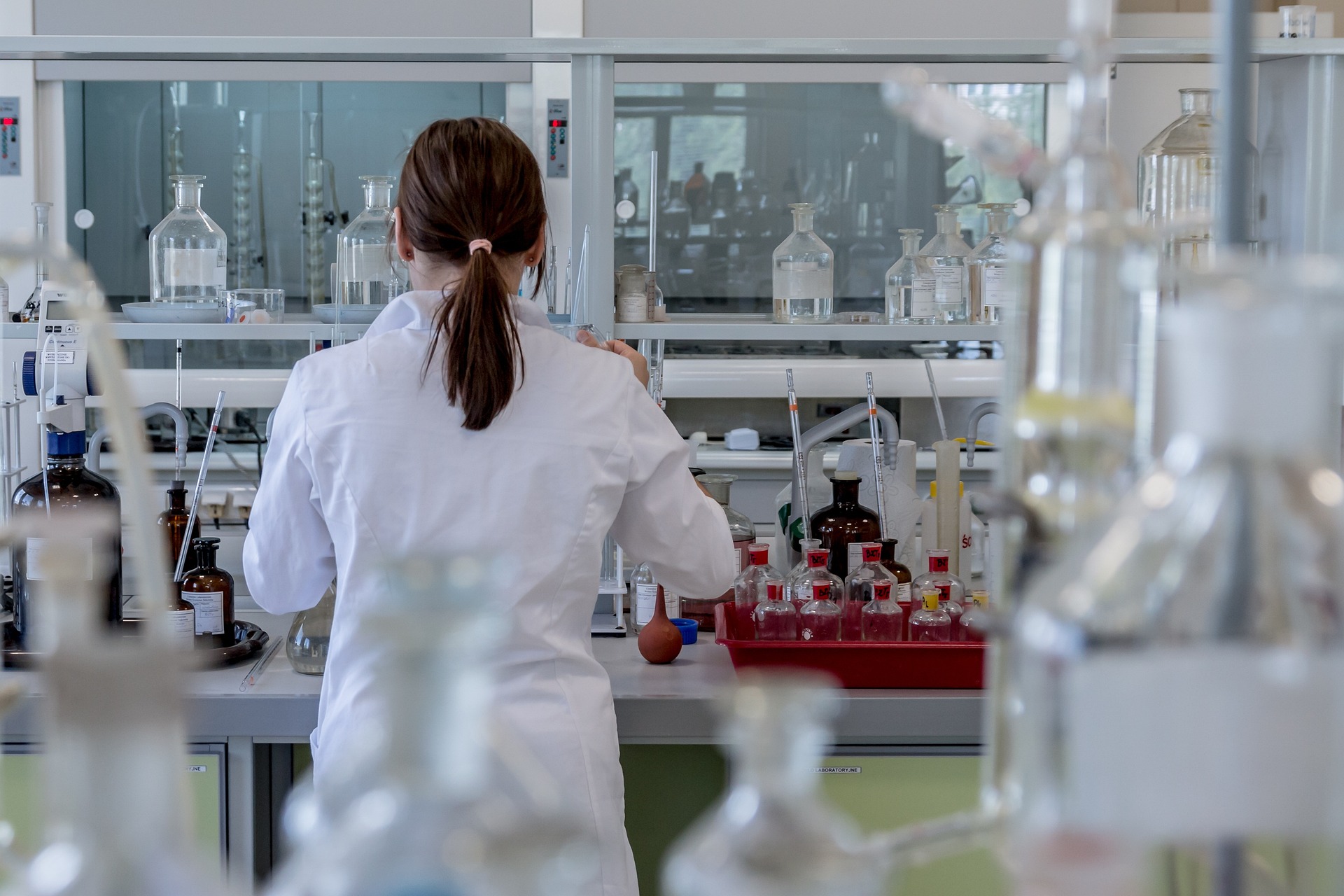
Public water systems that don’t monitor for PFAS have three years to start, under new U.S. Environmental Protection Agency rules that seek to remove “forever chemicals” from drinking water. Water utilities that want to automate this process should consider seeking help from a third-party.
February 7, 2024
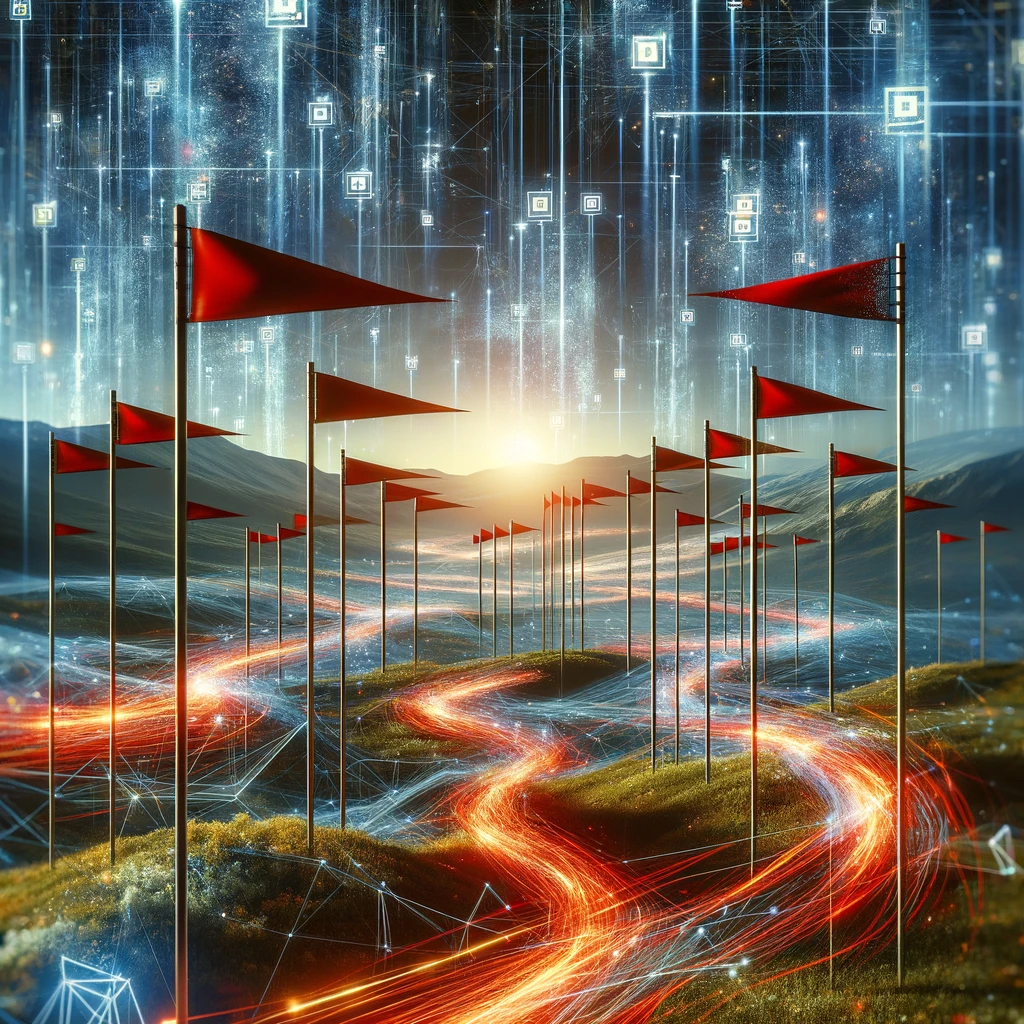
A new Cybersecurity & Infrastructure Security Agency guide goes beyond explaining how water/wastewater organizations should respond to cybersecurity incidents. It highlights six warning signs that administrators […]
December 11, 2023
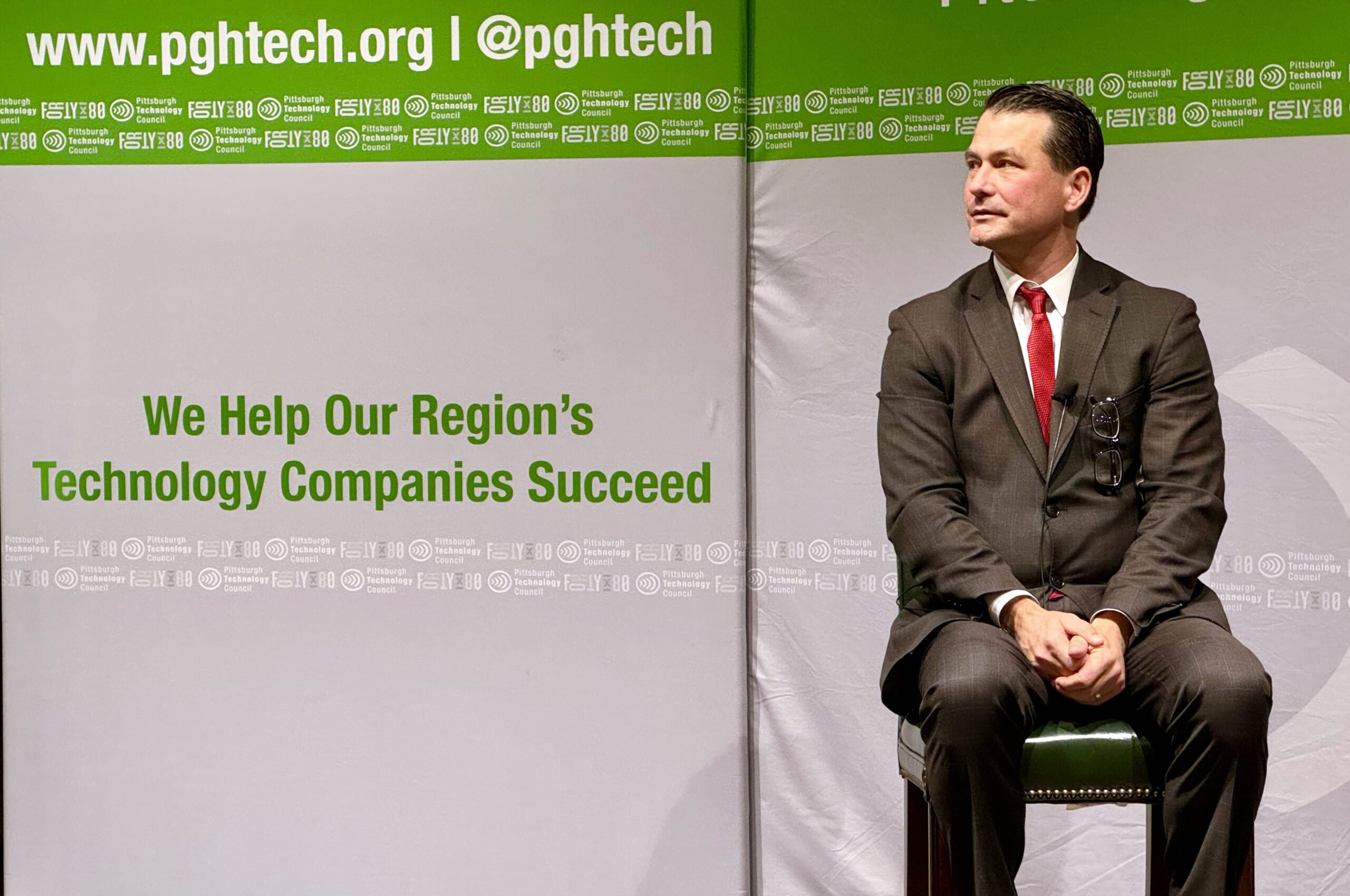
The White House is making a “once in a lifetime” investment in cybersecurity protections, but it’s up to critical infrastructure organizations to tap into it quickly […]
December 4, 2023
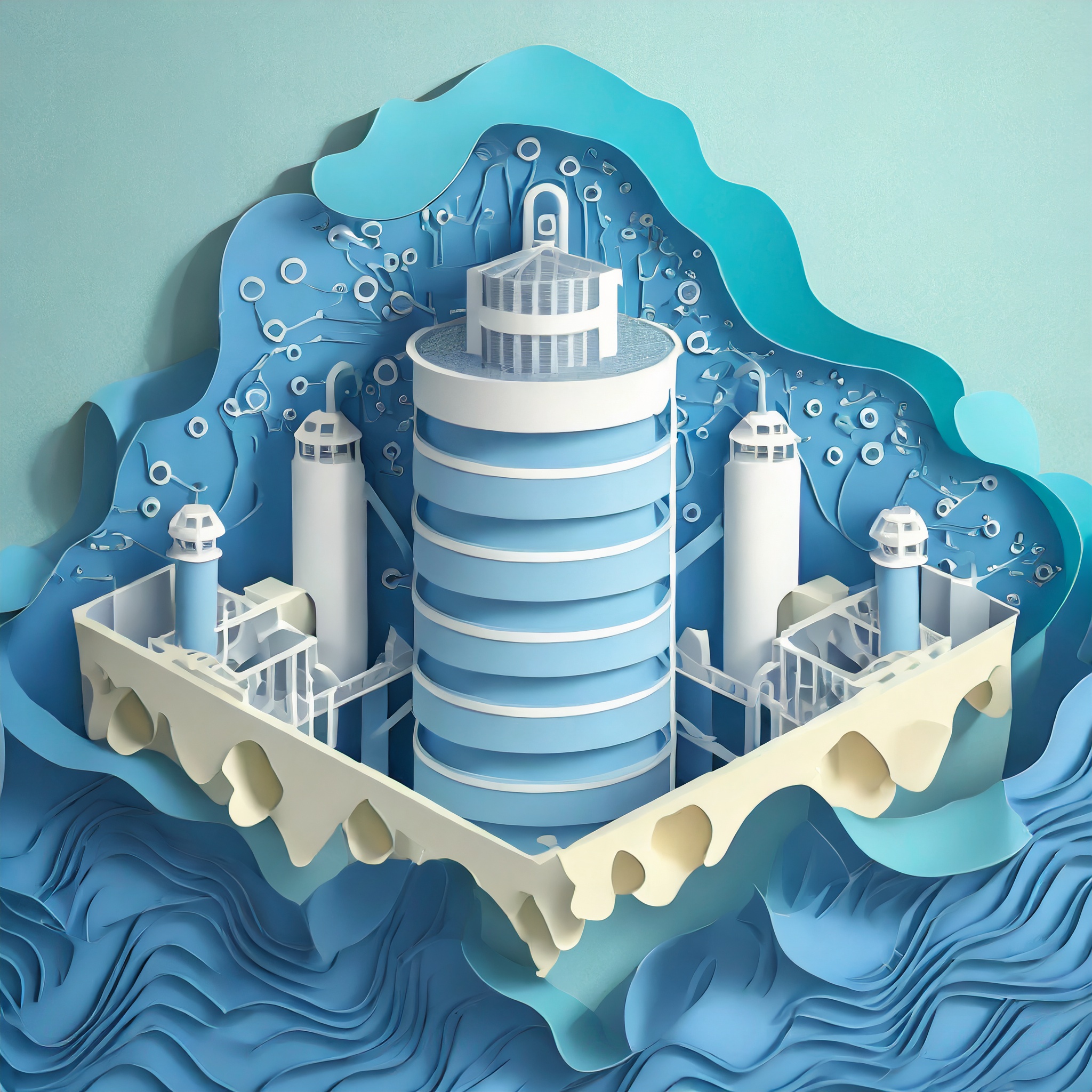
February 6, 2023
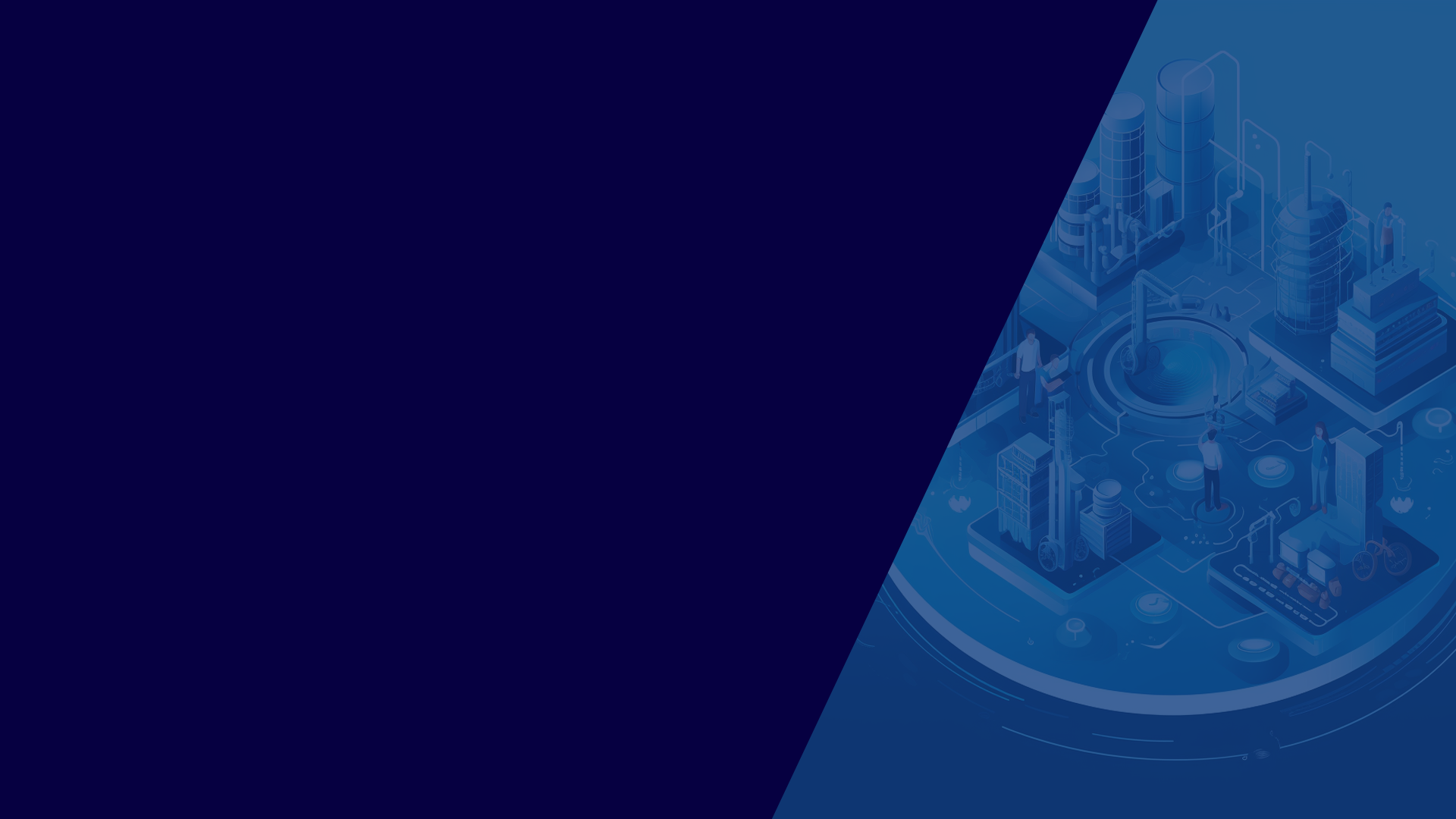
It's a big deal in cyber circles that NIST-CSF is poised to add a new function — Govern — to its well-known, five-part framework.
February 2, 2023
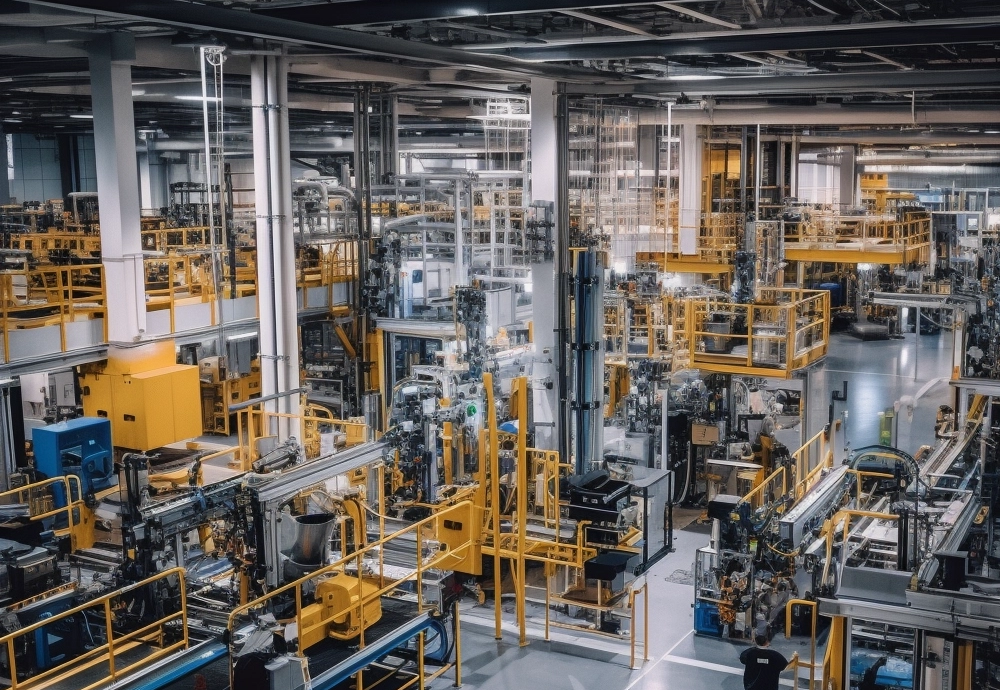
Industrial Technology Sector Grows During Economic Downturns: ‘Saving money never goes out of style.’ Technical.ly Pittsburgh interviewed CEO Jim Gillespie about GrayMatter’s latest strategic merger and […]
January 31, 2023

The Collier County Solid & Hazardous Waste Division held a ribbon-cutting ceremony in January 2023 to recognize the work and expertise that went into designing a “cost-effective, eco-friendly and long-term solution” that’s projected to save Collier County taxpayers $1.5 million a year.
December 5, 2022
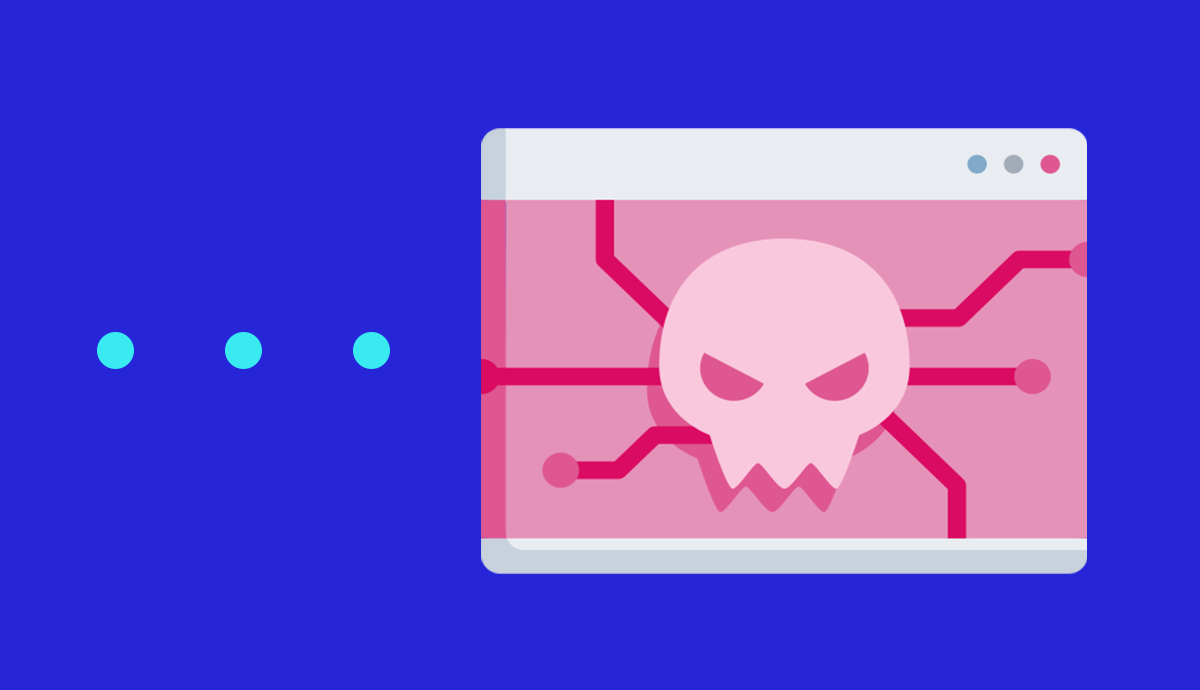
March 31, 2022
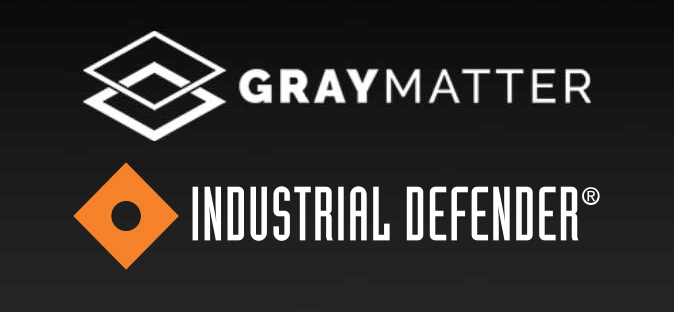
GrayMatter & Industrial Defender Equip Energy, Water Industries with Holistic Cybersecurity Defenses
This collaboration unites Industrial Defender’s comprehensive OT cybersecurity solution with GrayMatter’s highly skilled digital transformation consultants. Pittsburgh, PA — GrayMatter, the top digital transformation services firm for […]
December 16, 2021
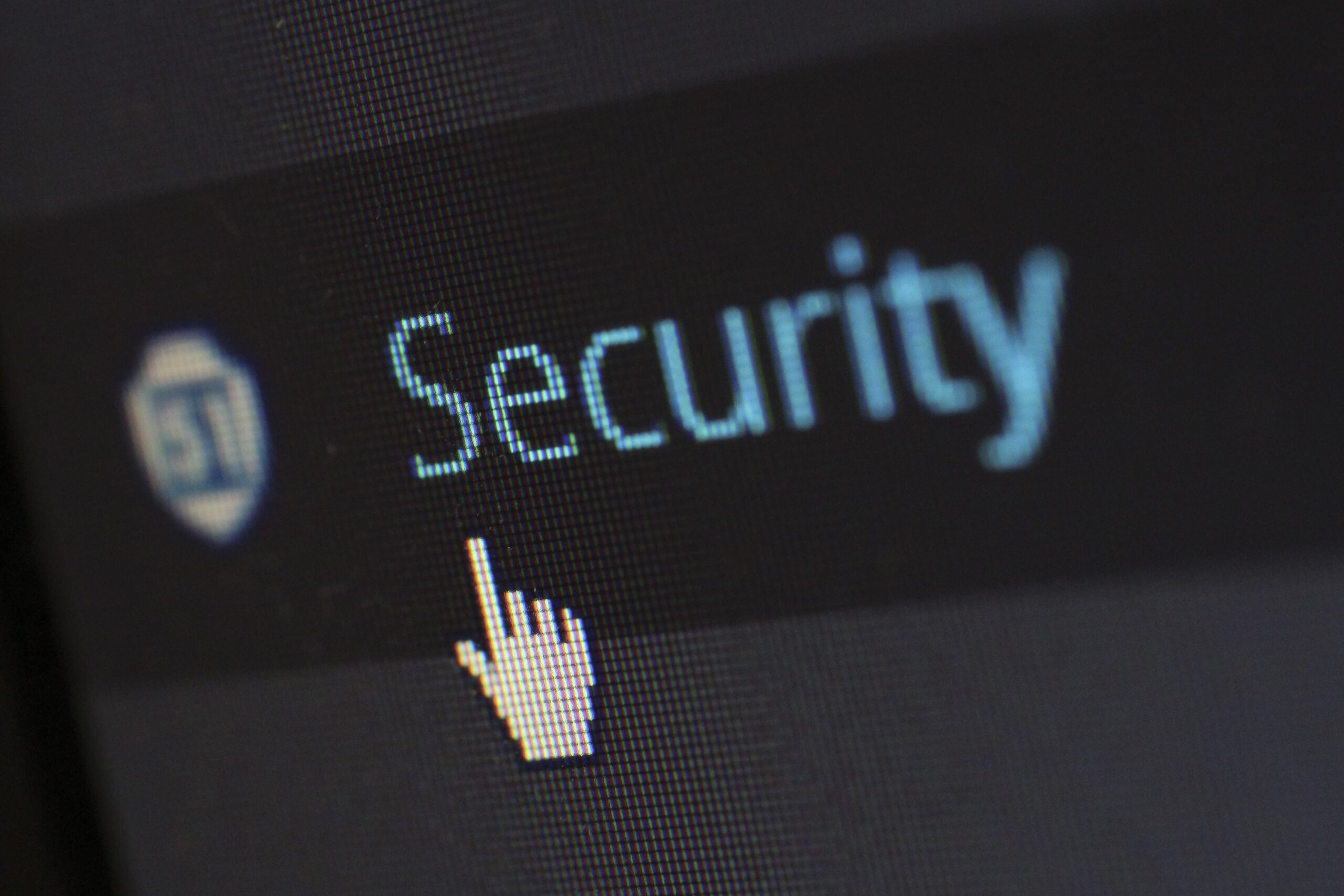
“With one line of code, this vulnerability can allow someone to remotely introduce malware into your network environment,” said Scott Christensen, GrayMatter’s Cybersecurity Practice Director.
Subscribe to TechHub
We know you’re busy.
Allow us to pore over top news and send you what impacts you the most. You’ll get instant access to our weekly TechHub roundup featuring top industry headlines, the latest customer stories and more, straight to your inbox.
Together, we’ll stay informed and empower our teams to work smarter in the changing world of operational technology. You can change your preferences at any time: