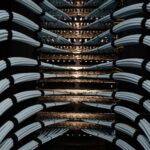
Data Centers Are Booming as Build Times & Power Needs Grow
March 18, 2025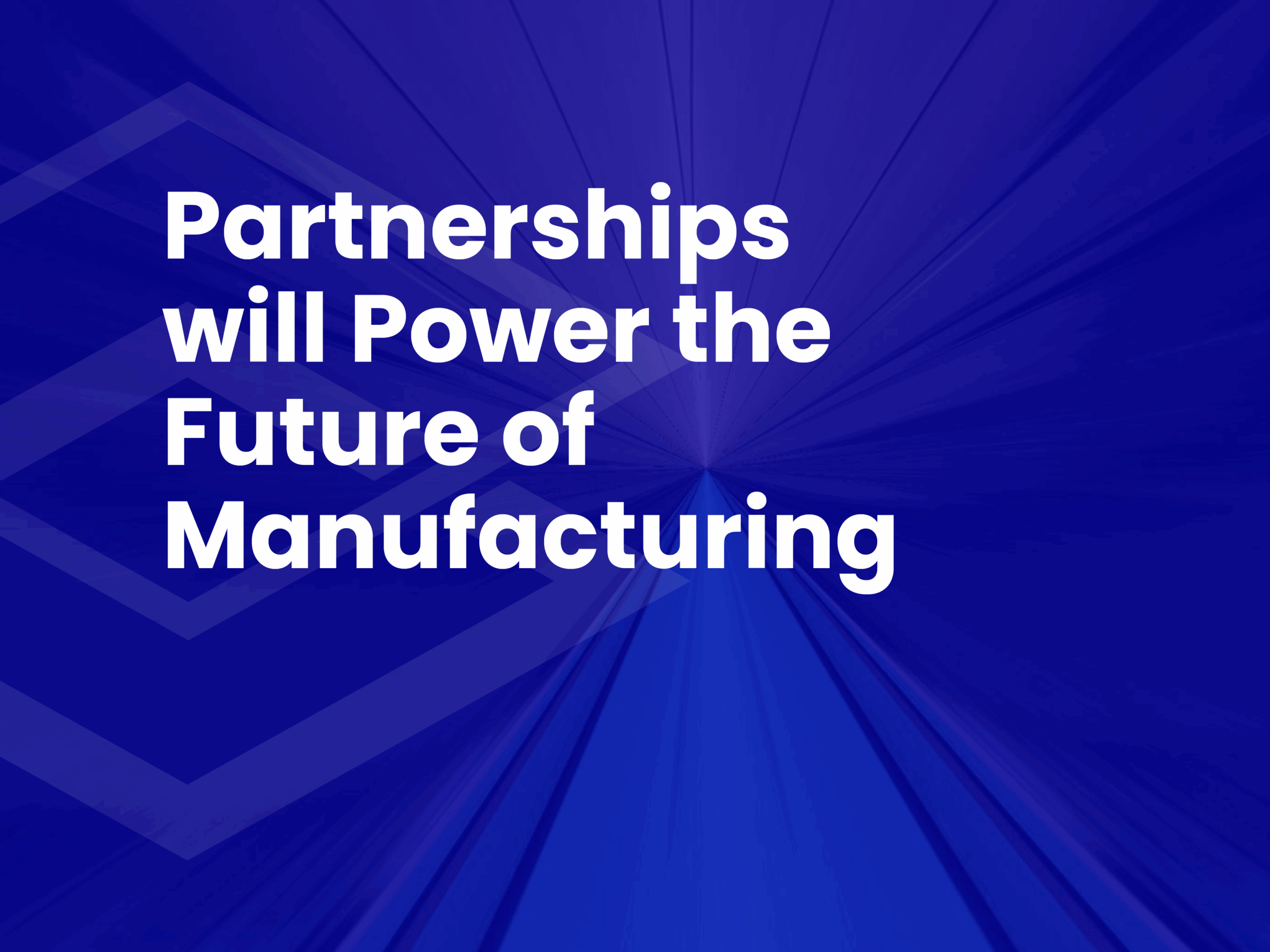
Partnerships Will Power Manufacturing’s Future
May 20, 2025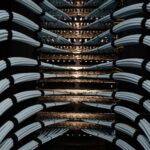
Data Centers Are Booming as Build Times & Power Needs Grow
March 18, 2025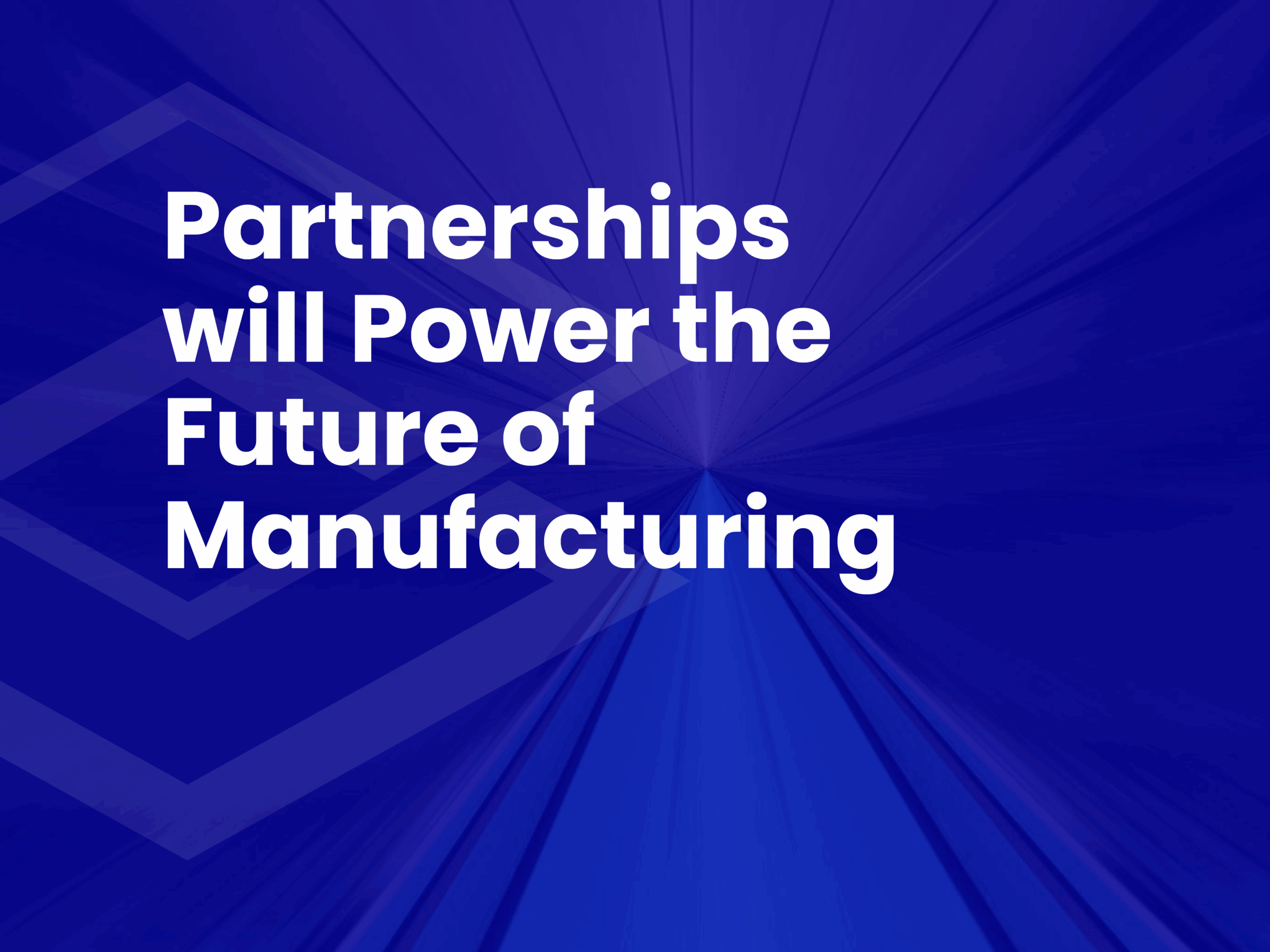
Partnerships Will Power Manufacturing’s Future
May 20, 2025Smart OEE Solution Unlocks Major Savings and Scalable Operational Control
A manufacturer that produces heat-resistant materials used in steelmaking, cement production and other heavy industries sought GrayMatter’s help to enhance its ability to analyze productivity metrics across its global network of sites.
What is OEE?
GrayMatter and the manufacturer worked together on an OEE (Overall Equipment Effectiveness) solution as part of GrayMatter’s Brilliant Operations offering, which enables manufacturers to increase their industrial data visibility, optimize existing processes and make smarter decisions.
OEE calculates the percentage of manufacturing time that is truly productive by measuring availability, performance and quality.
A perfect score would be 100% – meaning a company is producing the most high quality products in the least amount of time, with no interruptions. (Manufacturing Tomorrow)
The Problem
The company needed a solution to standardize OEE data across its facilities. Each site was using different units of measure (e.g., pounds vs. pieces), which made it difficult to compare performance metrics and identify inefficiencies.
The company lacked a centralized system for monitoring and analyzing downtime, leading to missed opportunities for optimization.
The Solution
GrayMatter implemented a multi-site OEE system that synchronized data from each site into a cloud-based platform, providing the manufacturer’s global team with a comprehensive view of efficiency metrics.
This solution includes integrating the company’s legacy systems with SCADA interfaces for standardized PLC controls and press layouts. The company uses presses to create large insulating blocks, which are used to create linings within forges and furnaces. The OEE system allows the company to categorize downtime events and pinpoint inefficiencies.
Over time, it has evolved to support a more scalable approach for managing work orders and improving product control, in alignment with management’s operations goals.
GrayMatter implemented
a multi-site OEE system that synchronized data from each site into a cloud-based platform.
Results
The OEE system led to immediate and measurable improvements.
Within the first two months, the company saved $800,000 by identifying and addressing major downtime events at one facility. This success prompted the company to expand the system to more sites, enabling it to gather consistent data and make better-informed decisions.
The project helped to create a global standard for measuring throughput, allowing the company to compare efficiency across plants and drive continuous improvement.
In Savings
Start a Project
Talk to Our Team of Experts
Monday - Friday
06:00 AM - 10:00 PM