COLGATE-PALMOLIVE
PREDICTIVE OPERATIONS INITIATIVE
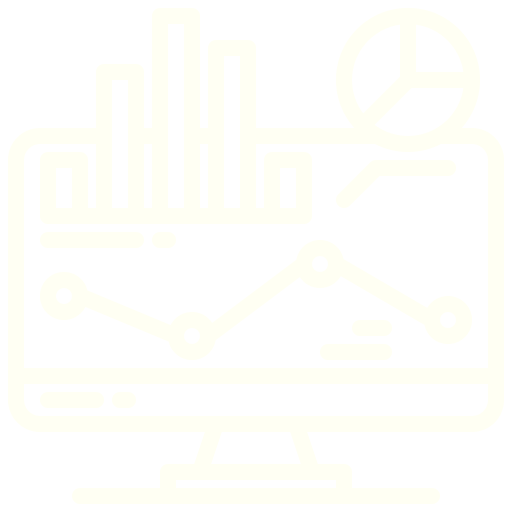
Creating Digital Twins
GrayMatter and Colgate-Palmolive co-innovate to create digital twins of extruders that Hill’s Pet Food Nutrition uses to produce thousands of pounds of dry pet food per day at facilities in Kansas and Indiana.
Digital Twins provide leaders and operators with intuitive visualizations and a means of comparing the operating costs and efficiency of machines, productions lines, shifts and entire facilities.
Ideal Startup Conditions
It requires roughly 50 minutes for pet food production to go from extrusion to a cooling tank, where quality sampling occurs.
When quality issues appear in a sample, the entire batch can be lost. Digital Twins enable operators to follow prescribed startup conditions that eliminate material waste and ensure a balance of four key factors in pet food production: fat, protein, moisture and density.
"Startup is where you have your biggest opportunity for absolute material loss and your biggest opportunity improve. We said, ‘Let’s get our startups right.’"
Darren Haverkamp, Technical Director, Hill’s Pet Nutrition
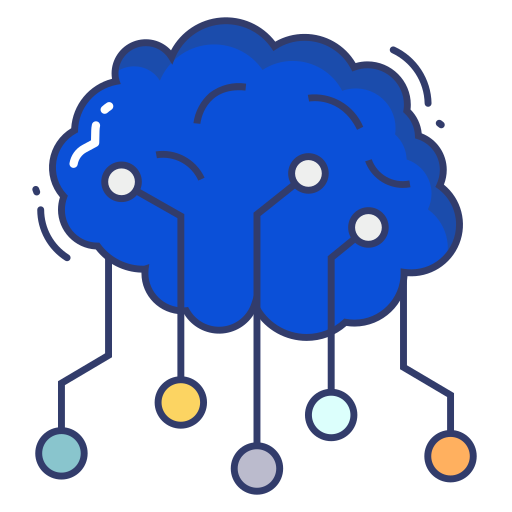
Big Wins
In-Process Adjustments
Machine-Learning Models based on historical production data from Digital Twins can now automatically make recommendations to operators about how to adjust production to ensure they maintain product quality and meet production goals.
This allows plant-floor personnel to fully operationalize data-driven insights and quickly adapt to frequent changes in product batch type, demand, ingredients and other variables.
Consistent Operator Performance
Challenge:
Predict Quality
Hill’s Pet Nutrition works with GrayMatter to reduce the amount of scrapped, out-of-spec product during startup and midline production.
Predictive Quality data modeling improves first-pass success and reduces reliance on lab test sampling. These are key business objectives as the number of SKUs increase and the quantities per SKU decrease.
How it Works
Predictive Quality application helps operators produce batches of pet food that meet content specs consistently. Using historical data, the predictive model provides recommendations to operators at startup and during operations about how to optimize product quality. The recommendations are based on the levels of fat, moisture, density and protein in the pet food. Real-time data visualizations show the current levels versus the ideal centerline. The application’s predictions have become so reliable that it now adjusts pet food extruder settings automatically (if desired) to keep to centerline.
Locations: Richmond, Ind., Emporia, Kan., Goa, India, Guatemala
Reduction in Energy Consumption by 2025
Challenge:
Predict Energy (WAGES)
Reducing electricity and water consumption tend to be the largest opportunities at manufacturing facilities that work with GrayMatter to cut WAGES-related costs.
To achieve company-wide energy goals, facilities must be able to compare energy utilization based on line, product and location to spot anomalies and identify opportunities to generate savings.
How it Works
Real-time dashboards benchmark and analyze energy consumption by asset, product group, production line and manufacturing site. Predictions, based on current and historical data, optimize usage of Water, Air, Gas, Electricity and Steam (WAGES), and can account for seasonal, pricing, staffing and other variabilities that impact energy costs.
Locations: Mission Hills, Mexico; Anchieta, Brazil
Improvement in Cycle Times
Challenge:
Predict Throughput
Reducing the time it takes to turn raw materials into finished products generates benefits throughout the supply chain, a priority as the consumer goods industry contends with rapid shifts in the consumer demand, resource availability and shipping times.
How it Works
Digital twins that represent physical manufacturing assets capture operations data such as product type, batch and phase. GrayMatter’s Predictive Quality and Predictive Throughput models ingest these data to train, troubleshoot and optimize solutions that improve operations in at three key ways: shorter cycle times, faster recipe development and more efficient recipe validation.
Locations: Goa, India
Improvement to Finishing OEE
Challenge:
Predict Throughput & Quality
OEE (Overall Equipment Effectiveness) is currently 70-75% as of 2021. Achieving an OEE of roughly 85% is considered by lean manufacturing experts to be a world-class level.
Predictive Throughput modeling allows organizations to reach that goal by capturing data about production uptime, quality and equipment performance, and testing methods to increase performance.
How it Works
Achieving a 10-point OEE improvement means carefully evaluating data points that affect availability, performance and quality. GrayMatter’s Predictive Uptime and Predictive Throughput applications produce insights into how product type, packing materials and machine setups influence OEE. Dashboards empower plant-floor operators to evaluate output from the applications.
Locations: Goa, India
“The benefits we see are going to be very large in terms of scrap production, quality improvements and yield.”
WARREN PRUITT, VP GLOBAL ENGINEERING SERVICES
ADVANCED ANALYTICS ONBOARDING
Adv. Industrial Analytics Onboarding includes guided steps to identify key stakeholders, identifying data sources for your manufacturing data, and getting prepared to provide an overview of the manufacturing process and equipment that will be modeled in your predictive operations platform.